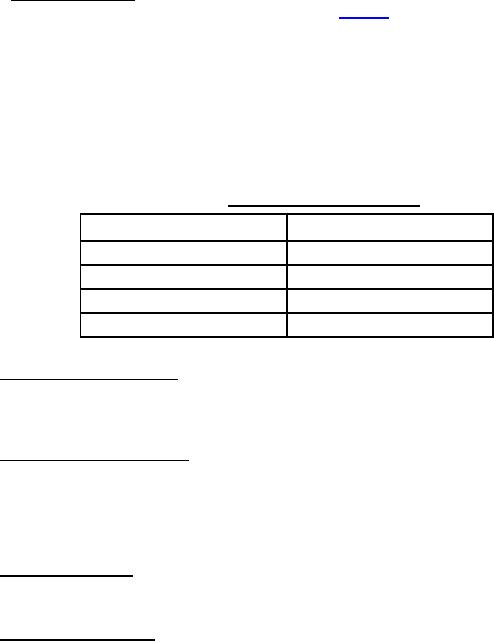
MIL-DTL-16356E
4.7.1.3 Seat tests (tightness). Valves shall be pressurized in the direction tending to open the valve and
examined for seat tightness. Test pressures shall be as specified in table IX. Stems shall be torqued to
17-23 foot-pounds. Duration of test shall be up to 15 minutes if leakage rate must be measured. There shall be no
visible signs of leakage. Should there be any visible leakage, this test shall be continued for 15 minutes to
accurately determine the rate of leakage. In checking leakage, three consistent measurements shall be made and
recorded for each test. Leakage shall not exceed the amount specified in 3.10.2.2. The maximum allowable force to
seat valves during this test shall be as specified in 3.10.2 and 3.10.3. When valve is depressurized, gland and
packing shall be removed. The stem shall be backseated to 17-23 foot-pounds of torque. The valve shall be
positioned so that leakage can flow by gravity through the stuffing box. The same test pressure durations and
leakage criteria as the main seat test shall apply to the back seat test.
TABLE IX. Test pressures for seat tightness.
ANSI Valve Ratings (psi)
Pressures (psig)
150 (Type C)
313
300 (Type B)
816
600 (Type A, Class I and II)
1629
1500 (Type A, Class IV)
4074
4.7.2 Hydrostatic test of ball-check. Each automatic ball-check valve selected as specified in 4.5.3 shall be
tested for leakage by hydrostatic pressure. Automatic ball-check valves shall seat automatically under the action of
escaping water, shall withstand a hydrostatic pressure of one and one-half times the designated pressure with
leakage of not more than 100 cm3 an hour, and shall open automatically upon release of pressure.
4.7.3 Gauge hydrostatic pressure test. Each gauge shall be subjected for at least 1 minute, maximum
10 minutes, with all valves except the drain valve open, to a hydrostatic pressure equal to the applicable design
pressure as a test of the strength and rigidity of the gauge for the pressure at which it is to be used. Glass and
gaskets used for this test and 4.7.4 steam pressure test below may be in accordance with the gauge manufacturer s
drawings and specifications for the gauge. Any leakage or distortion shall be considered cause for rejection of the
gauge being tested.
4.7.4 Gauge steam pressure. Each gauge shall be subjected for at least 1 minute, maximum 10 minutes, with
all valves except the drain valve open, to the applicable design pressure. Any leakage or distortion shall be cause for
rejection of the gauge being tested.
4.7.5 Valve stem hardness tests. The manufacturer shall perform a Rockwell hardness test on all finished stems
after heat treatment. Testing shall be limited to the sheave wheel end of the stem, the stem square, and the surface
defined by the packing diameter, within ½ inch of the Acme threads. The stem hardness shall consist of three
hardness readings taken at any combination of locations specified above. The hardness criterion of 803-2177525
shall be used to determine acceptability of stem hardness.
26
For Parts Inquires call Parts Hangar, Inc (727) 493-0744
© Copyright 2015 Integrated Publishing, Inc.
A Service Disabled Veteran Owned Small Business