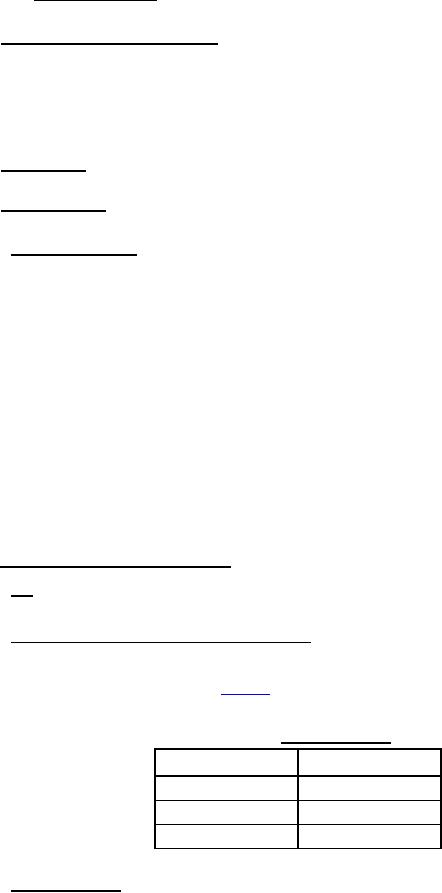
MIL-DTL-16356E
4.4.1.8.2 Compression testing. The following tests shall be done on selected bolt assemblies or individual
washers as indicated:
a. Load-deflection test (bolt assembly). It must be verified that washers are in proper parallel-series sequence.
Collars need not be installed. Each sample shall be compressed on a tensile test machine or equivalent rigid test
frame calibrated for the accuracy required. Results must be adjusted to eliminate deflection of the test frame or
machine compliance of the tensile machine. The bolt specimen shall be supported in a hollow cylinder that fully
supports the washer while permitting compression of the washers. The test fixture cannot interfere with the portion
of the bolt that extends below the washer stack. Curves of compression load (in pounds) versus deflection of the
three bolt assembly washer stacks over the range of 0 to 0.040 inch deflection shall be generated.
b. Permanent set. Three individual washers shall be deflected to 0.140 inch overall height (⅔ of the formed
height). Before and after the test the overall height shall be measured.
c. Repeated loading. Three individual washers shall be deflected 10 times from free height to within 0.004 to
0.006 of solid height (flat) and visually inspected.
4.4.2 General examination. The gauge assemblies with valves, if applicable, shall be subjected to a thorough
examination to determine that the material, workmanship, safety to operating and maintenance personnel, design,
and construction are in conformance with this specification and applicable drawings. Examination shall include, but
not be limited to, the following:
a. Verification that the arrangement of body sections, nipples, valves, insert recesses, chamber passages, and
covers and cover clamping devices meet specific requirements for the gauge type. Verification that the required
visibility is provided for the gauge type.
b. Verification that fasteners and locking devices are of the correct type, and that thread protrusion beyond
nuts meets requirements. Inspection for coating and plating that may be either required or prohibited on fasteners.
Inspection for tack welds required by 3.6.
c. Verification that gasket seating surfaces on gauges, flanges (including nipples), and valves are suitable for
the specified gasket materials based on surface finish requirements herein. This inspection will also include valve
packing gland design and suitability for the required packing materials.
d. Verification of the compatibility and fit of closed illuminators or other attached light assemblies and valve
sheave wheels with chain guides. Verification that illumination devices have the same hardware arrangement as
tested under 4.5.1 and fit securely to gauge body.
4.5 Sampling for conformance inspection.
4.5.1 Lot. All items of the same type, configuration class, length, composition, size, and pressure rating
(see 1.2) presented for delivery at one time shall be considered a lot.
4.5.2 Sampling for visual and dimensional examination. A random sample of items, except Type A shut-off
valve assemblies, shall be selected from each lot for examination of visual and dimensional characteristics in
accordance with ASQ H1331 at Inspection Level III. These sample items shall be examined as specified in 4.6.
Sample size for valve assemblies is shown in table VI.
TABLE VI. Valve sample size.
Lot Size
Sample Size
2 to 25
1
26 to 65
2
66 to 180
3
4.5.3 Sampling for tests. A random sample of items shall be selected from each lot in accordance with
ASQ H1331 at Inspection Level III for the tests specified in 4.7.
24
For Parts Inquires call Parts Hangar, Inc (727) 493-0744
© Copyright 2015 Integrated Publishing, Inc.
A Service Disabled Veteran Owned Small Business